TO READ THE FULL STORY:
LOG IN
Digital Access
$4.99 /month or $49.99 /year
SAVE $10 | Yearly Subscription
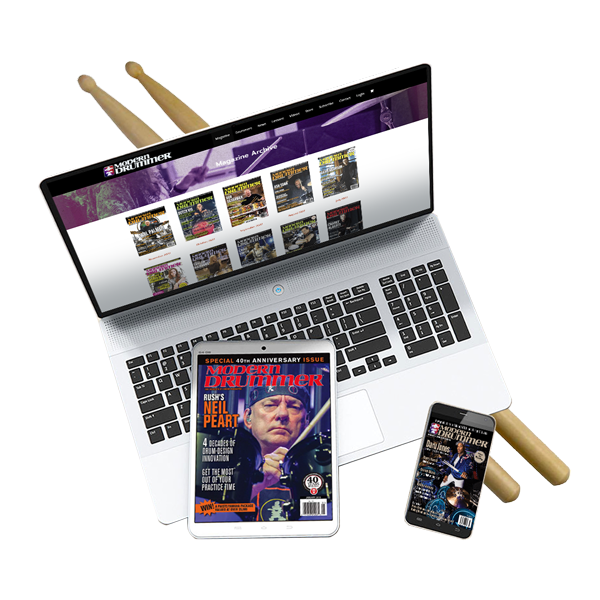
- 49+ Years of Archives
- 500+ Back Issues
- Drum Channel Lesson Videos
- Interviews, Lessons & Gear Reviews from Drum Legends
DigiPrint subscription
USA $179.99 / year (Billed Annually)
USA $14.99 /Month
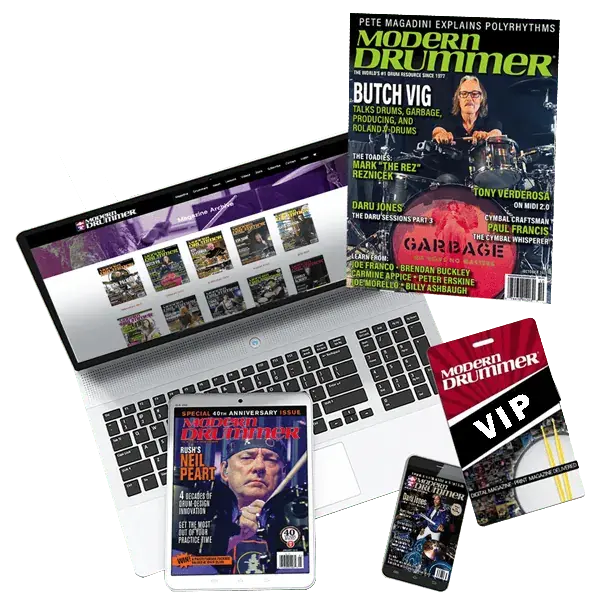
Get ALL ACCESS – both digital and print
Meet DigiPrint – a collectible physically condensed magazine focusing on the cover story with virtually limitless digital access via QR codes.
All-Access includes:
- 🎁 Everything in Digital Access +
- 🖥 6 Collectible Print Magazines Per Year
- 📰 12 Monthly Digital Issues Per Year
- 📱 Exclusive Video Content
- 📱 $30 MD gift card for books, merch, or lessons!
googletag.cmd.push(function() {
googletag.defineSlot(
'/134312942/MOD_ROS_DES_MPU',
[300, 250],
'ad_300_250_3'
).addService(googletag.pubads());
});
Advertisement
googletag.cmd.push(function() { googletag.display('ad_300_250_3'); });